[The high aluminum cement products introduction ] :
Also known as alumina cement, high alumina cement refractory cement, aluminate cement, collectively known as aluminate cement, bauxite and limestone as raw material, after the calcination of calcium aluminate as main ingredients, alumina content is about 50% of the clinker, again into the water rigid gelled material. High alumina cement is often yellow or brown, and gray. With a rapid hardening, early strength, corrosion resistance, resistance to high temperature of the water rigid gelled material; It is a kind of high-quality building materials, is also a kind of loose refractory for gelling property, in metallurgy, building materials, oil chemical, electric power, food and other industries has been widely used.
[product technical requirement]:
1, fineness, cement particle is fine, the bigger the specific surface area, the faster the hydration reaction more fully, the early and late strength is higher. The provisions of the state: the specific surface area should be more than 300 square meters/kg, otherwise is unqualified.
2, setting time, in order to guarantee the construction have enough time to complete mixing, transportation, forming a variety of craft, such as the initial setting time of cement shoulds not be too short; After the completion of the engineering project, the hope cement hardening, as soon as possible to produce strength, so the final setting time shoulds not be too long. The initial setting time of Portland cement shall not be earlier than 45 minutes, final set time not later than 390 minutes.
3, volume stability, water slurry uniformity of volume change in the process of condensation sclerosis called the volume stability of cement. Such as volume change uneven or volume stability, prone to warping and cracking, reduce the engineering quality and even an accident.
4, refractory cement refractory cement lining for baking, must pay attention to the following matters:
Stage 1) under normal temperature 350 degrees, the most easily cause local burst, it is important to pay special attention to the slow roasted. If there are still a lot of steam after 350 degrees heat preservation, should still slow heating speed.
2) under the condition of poor ventilation, water discharge, should be appropriately extended holding time.
3) when using heavy oil baking, carefully crude oil is sprayed on the surface of lining, in case of partial burst.
4) when use firewood baked, direct contact with the flame place often causes local warming too rush, should be protected.
5) cast of new refractory cement, at least by 3 d can be carried out only after baking.
6) for refractory cement lining cooling should also slow, avoid forced ventilation.
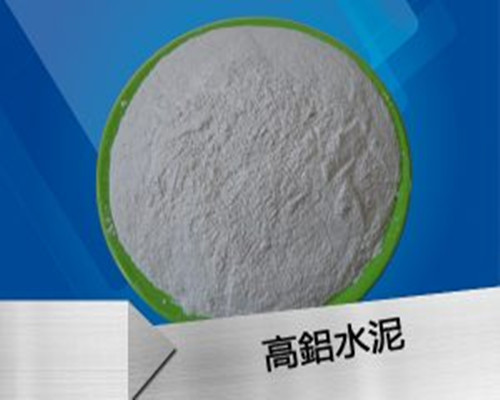