Type: | Hybrid |
---|---|
Phase: | 2 |
Current / Phase: | 3.0A |
Brand Name: | KIMBROUGH |
Step Angle(degrees): | 1.8 |
Model Number: | J57HB56-03 |
Certification: | CE |
Holding Torque: | 0.9N.m(129oz-in) |
Motor Model Number: | J57HB56-03 |
Matched driver: | JB542M |
Motor length: | 56mm |
Lead wire: | 4 wires |
Place of Origin: | Guangdong, China (Mainland) |
Application 1: | CNC Router Plastic Mill |
Application 2: | Laser machine |
is_customized: | Yes |
Unit Type: | Set |
Package Size: | 25cm x 15cm x 15cm (9.84in x 5.91in x 5.91in) |
Package Weight: | 3.5kg (7.72lb.) |
Quick Details
Specifications
2 Axis CNC NEMA 23 Jingbo stepper motor J57HB56-03 129oz-in and Driver JB542M 4.0A DC20-50V 200Micro laser machine 3D printer
This item includes :
2 PCS NEMA23 hybrid stepper motor J57HB56-03 single shaft 0.9N.m(129oz-in) 3.0A 56mm
2 PCS stepper motor driver JB542M 4.0A DC20-50V 200Microsteps
1 Stepper motor
General specifications
Step Angle Accuracy: 5%
Temperature rise: 80°c Max
Ambient temperature: -20°c~+50°c
Insulation resistance: 100MΩ Min 500VDC
Dielectric strength: 500V AC 1minute
Shaft Radial Play: 0.02mm Max(450g-load)
Shaft Axial Play: 0.08mm Max(450g-load)
Specifications:
Model | Step Angle (°) | Length L(mm) | Holding Torque (N.m) | Current (A/Phase) | Resistance (Ω) | Inductance (mH) | Rotor inertia (g.cm2) | Weight (kg) | Shaft diameter (mm) | Axis stretch (mm) | Lead wire |
J57HB56-03 | 1.8 | 56 | 0.9 | 3.0 | 0.75 | 1.1 | 300 | 0.7 | 6.35/8.0 | Leveling block 0.5x20 | 4 wires |
Only the representation of the products, we can design according to clients’ requirement
Note: If you don't specify, we will ship you the motor with 6.35mm shaft diameter by default
Dimension: unit=mm
Frequency-torque characteristics
Wiring Diagram
Installation precaution
- Data of electrical characteristics and technical data are both measured by JB542M driver, testing voltage DC28V.
- When motor mounted, be sure its front cover should be installed to the seam allowance position and attention to the fit tolerance and strictly ensure that the concentricity of electrical motor axis with the load.
- Please do not connect wrong phase when fitting the motor and driver.
Stepper motor driver JB542M 4.0A DC20-50V 200Microsteps
Features
High performance, low price
16 channels constant angle and constant torque microstep, max revolution is up to 40000 pulse/R
Upmost response frequency amounts to 200Kpps
Once the pulse stops over 1.5s, the phase current will be automatically reduced to half of pre-set current
Opto-isolated signal Input/Output
Driving current can be adjusted from 1.0A/phase to 4.0A/phase through 8 channels
Single power input, voltage range: DC20-50V
It can match 2 phase hybrid stepper motors whose current is under 6.0A, flange size ranges from 42mm to 86mm.
Wiring and Dimension example
Current setting
The working current of the driver is set by SW1-SW3 terminal, for more details please refer to the diagram below .
Current (A) | 1.0 | 1.2 | 1.5 | 2.0 | 2.5 | 3.0 | 3.5 | 4.0 |
SW1 | ON | OFF | ON | OFF | ON | OFF | ON | OFF |
SW2 | ON | ON | OFF | OFF | ON | ON | OFF | OFF |
SW3 | ON | ON | ON | ON | OFF | OFF | OFF | OFF |
The SW4 is used to set Half current/Full current: OFF=Half Current ON=Full current
Microstep setting
The microsteps of the driver are set by SW5-SW8 terminal with the following 16 channels. Details are as below: Microsteps(pulse/R)
Microstep | 200 | 400 | 800 | 1600 | 3200 | 6400 | 12800 | 25600 |
SW5 | ON | OFF | ON | OFF | ON | OFF | ON | OFF |
SW6 | ON | ON | OFF | OFF | ON | ON | OFF | OFF |
SW7 | ON | ON | ON | ON | OFF | OFF | OFF | OFF |
SW8 | ON | ON | ON | ON | ON | ON | ON | ON |
Microstep | 1000 | 2000 | 4000 | 5000 | 8000 | 10000 | 20000 | 40000 |
SW5 | ON | OFF | ON | OFF | ON | OFF | ON | OFF |
SW6 | ON | ON | OFF | OFF | ON | ON | OFF | OFF |
SW7 | ON | ON | ON | ON | OFF | OFF | OFF | OFF |
SW8 | OFF | OFF | OFF | OFF | OFF | OFF | OFF | OFF |
Note: The microsteps can be customized according to clients’ requirement.
Terminal function
Mark | Function | Notes |
PU+ | Step pulse signal+ | It can connect +5V or +28V, and an extra resistor is not needed if it connect +28V |
PU- | Step pulse signal- | Effects on falling edge, the motor goes one step as the pulse input change from “high” to “low”. Input resistance is 220Ω. Requirement: low voltage:0-0.5V, high voltage:4-5V, pulse width >2.5μs |
DR+ | Direction control signal+ | It can connect +5V or +28V, and an extra resistor is not needed if it connect +28V |
DR- | Direction control signal- | Change motor’s direction of rotation. Input resistance is 220Ω. Requirement: low voltage:0-0.5V, high voltage:4-5V, pulse width >2.5μs |
MF+ | Motor Free signal+ | It can connect +5V or +28V, and an extra resistor is not needed if it connect +28V |
MF- | Motor Free signal- | Once effects, it will cut off the motor current, the driver stops working and sets the motor free |
V- | Power- | DC20-50V |
V+ | Power+ | |
A+ |
Connect to the motor | |
A- | ||
B+ | ||
B- |
! Caution
1.The input voltage can not exceed DC50V .
2.Input control signal ranges from +5V to +28V, current-limiting resistance is not needed when it is over +5V.
3.The input pulse signal effects on falling edge
4.ALM lights and the driver stops working when the driver temperature is over 80C. Until the temperature falls to 50C, it will restart to work after powered-up. The heat sink is needed when overheat occurs
5.ALM lights if it is short circuit, please check motor leads and eliminate other short faults, and then repower up to restore
6.ALM lights if the motor does not connect well with the driver, please check motor leads and repower up to restore
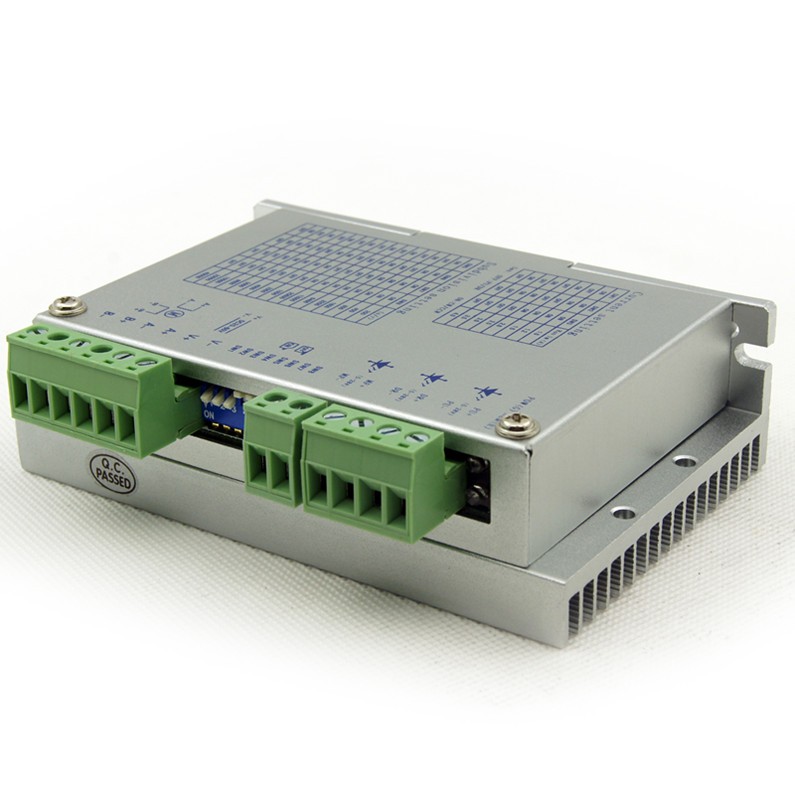