After-sales Service Provided: | No overseas service provided |
---|---|
Certification: | CE |
Brand Name: | LNEYA |
Type: | Compressor |
Refrigerant: | 1-115 |
Quick Details
Specifications
in the following key areas, the operation of the device is superior:
1. Storage area: air evaporation loss of empty valve;
2. Loading and unloading area: the tank car exhausts the evaporation loss;
3. Production drop zone: pull-tank, stirring reaction kettle solvent volatilization loss;
4. Recovery of volatile VOCS gases produced by various volatile chemical loading, chemical storage and transportation, chemical and pharmaceutical industries.
Principle of condensing process:the volatile VOCS gas is imported into the equipment cooler (the maximum setting of condensing temperature of the device is 3), and the other temperature zones can be customized to follow up the demand for cooling and liquefaction.Partial continuous production process has been made in the low-temperature section of the two-circuit switching process (one side of the ice is blocked, but the other one is directly changed to the other way, the cold box is condensed, and the ice block is used for the defrost treatment).
Technical parameters:1. Gas handling capacity: 100m3/h ~ 2500m3/h.
5m3/h 100m3/h 300m3/h 400m3/h 800m3/h 800m3/h 1,500m3 /h 2000m3/h.
2. Operating power: 3kw ~ 300kw.
3. System pressure difference: 250pa ~ 450pa.
4, the lowest temperature: 1 and 40 to 75 to 115
5. Explosion-proof type: positive pressure EXpxdmbII BT4.
6. Unit energy consumption: 3 -40 -40 -75 - grade iii temperature condensation recovery is greater than 100m3/h.
the three-stage condensing recovery unit consumes less than 0.2kw/m3.
(this indicator varies slightly depending on ambient temperature, humidity, site conditions and solvent gas concentrations)
Exhaust emission: for the recovery and treatment of solvent gas, the exhaust emission standards of 20g/m3 can be met according to the requirements;If there is a low boiling point gas in the gas (the condensation does not liquefy), the process of adsorption and membrane treatment of activated carbon can be separated and treated again, so that the emission gas can meet the environmental requirements.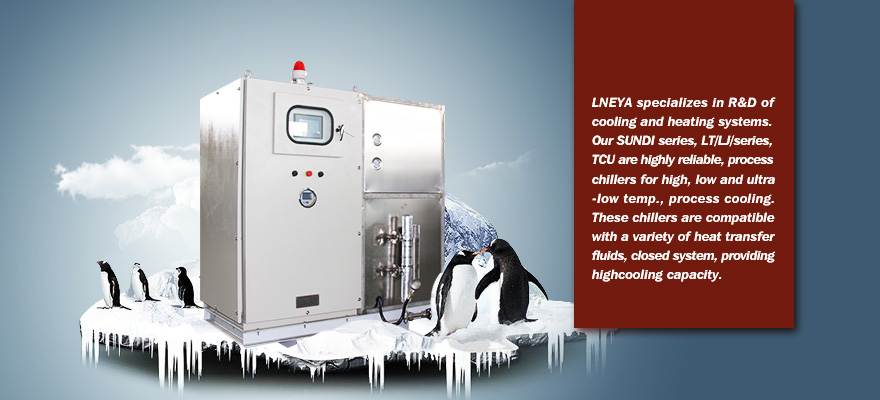
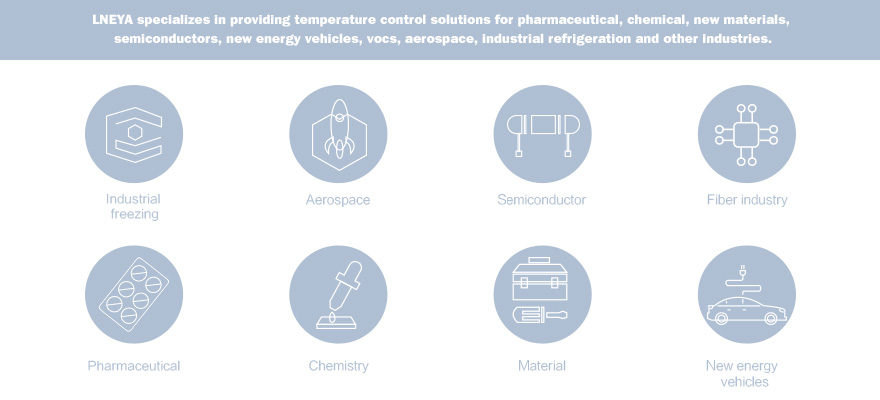
1. Storage area: air evaporation loss of empty valve;
2. Loading and unloading area: the tank car exhausts the evaporation loss;
3. Production drop zone: pull-tank, stirring reaction kettle solvent volatilization loss;
4. Recovery of volatile VOCS gases produced by various volatile chemical loading, chemical storage and transportation, chemical and pharmaceutical industries.
Principle of condensing process:the volatile VOCS gas is imported into the equipment cooler (the maximum setting of condensing temperature of the device is 3), and the other temperature zones can be customized to follow up the demand for cooling and liquefaction.Partial continuous production process has been made in the low-temperature section of the two-circuit switching process (one side of the ice is blocked, but the other one is directly changed to the other way, the cold box is condensed, and the ice block is used for the defrost treatment).
Technical parameters:1. Gas handling capacity: 100m3/h ~ 2500m3/h.
5m3/h 100m3/h 300m3/h 400m3/h 800m3/h 800m3/h 1,500m3 /h 2000m3/h.
2. Operating power: 3kw ~ 300kw.
3. System pressure difference: 250pa ~ 450pa.
4, the lowest temperature: 1 and 40 to 75 to 115
5. Explosion-proof type: positive pressure EXpxdmbII BT4.
6. Unit energy consumption: 3 -40 -40 -75 - grade iii temperature condensation recovery is greater than 100m3/h.
the three-stage condensing recovery unit consumes less than 0.2kw/m3.
(this indicator varies slightly depending on ambient temperature, humidity, site conditions and solvent gas concentrations)
Exhaust emission: for the recovery and treatment of solvent gas, the exhaust emission standards of 20g/m3 can be met according to the requirements;If there is a low boiling point gas in the gas (the condensation does not liquefy), the process of adsorption and membrane treatment of activated carbon can be separated and treated again, so that the emission gas can meet the environmental requirements.