Surface Finishing: | Immersion Gold |
---|---|
Board Thickness: | 1.6mm |
Copper Thickness: | 35 um (1oz) |
Base Material: | Polyimide |
Brand Name: | Bicheng Enterprise Limited |
Min. Line Spacing: | N/A |
Min. Line Width: | N/A |
Min. Hole Size: | N/A |
Model Number: | BIC-259-V259 |
Place of Origin: | China (Mainland) |
Solder Mask Color: | Yellow / Green Solder mask |
Colour of Component Legend: | White |
TEST: | 100% Electrical Test prior shipment |
Quick Details
Specifications
Structure of FPC
According to the number of layers of conductive copper foil, FPC can be divided into single
Layer circuit, double layer circuit, multi-layer circuit, double sided and so on.
Single-layer structure: the flexible circuit of this structure is the simplest structure of the
Flexible PCB. Usually the base material (dielectric substrates) + transparent rubber(adhesive)
+ copper foil is a set of purchased raw materials(semi-manufactures), the protective film and
Transparent glue are another kind of bought raw material. First, copper foil must be etched to
Obtain the required circuit, and the protective film should be drilled to reveal the corresponding
Pad. after cleaning, the two are combined by rolling. Then the exposed part of the pad
Electroplated gold or tin to protect. In this way, the big panel board will be ready. Generally
Also it's stamped into the corresponding shape of the small circuit board. There is also no
Protective film directly on the copper foil, but printed resistance soldering coating, so that the
Cost will be lower, but the mechanical strength of the circuit board will become worse. unless
the strength requirement is not high and the price needs to be as low as possible, it is best to
Apply the protective film method.
Double layer structure: when the circuit is too complex to be wired, or copper foil is needed
to shield the ground, it is necessary to choose a double layer or even a multilayer. the most
Typical difference between a multilayer and a single plate is the addition of a perforated structure
to connect the layers of copper foil. the first process of transparent rubber + base material +
Copper foil is to make holes. Drill holes in the base material and copper foil first, clean and then
Plated with a certain thickness of copper. the subsequent fabrication process is almost the same
as the single-layer circuit.
Double sided structure: both sides of the double sided FPC have pads, mainly used to connect
Other circuit boards. Although it and monolayer structure is similar, but the manufacturing
Process is very different. Its raw material is copper foil, protective film and transparent glue.
the protective film should be drilled according to the position of the pad first, then the copper
Foil should be affixed, the pad and track lines should be etched and then the protective film
of another drilled hole should be affixed.
Copper foil is available in two different types of copper: ED Copper and RA copper.
ED copper is an electro-deposited (ED) copper foil produced in the same way as the copper
Foil used for rigid printed circuit boards. this also means that the copper is " treated", i.e., it
Has a slightly rough surface on one side, which ensures a better adhesion when the copper
Foil is bonded to the base material.
RA copper is a rolled and annealed copper foil produced from electrolytically deposited cathode
Copper, which is melted and cast into ingots. the ingots are first hot-rolled to a certain size and
Milled on all surfaces. the copper is then cold-rolled and annealed, until the desired thickness
Is obtained.
Copper foil is available in thickness of 12, 18, 35 and 70 m.
the most common available for dielectric substrate and coverlay is polyimide films. this
Material can also be used as coverlay. Polyimide is best suited for flexible circuits because
of its characteristics as stated below:
High temperature resistance allows soldering operations without damaging the flexible
circuits
Very good electrical properties
Good chemical resistance
Polyimide is available in thicknesses of 12.5, 20, 25 and 50 m.
Base laminates for rigid printed circuit boards are copper foils laminated together with the
Base materials, the adhesive coming from the prepreg material during lamination. Contrary
to this is the flexible circuit where the lamination of the copper foil to the film material is
Achieved by means of an adhesive system. It is necessary to distinguish between two main
Systems of adhesive, namely thermoplastic and thermoset adhesives. The choice is dictated
Partly by the processing, and partly by the application of the finished flexible circuit.
FPC Case: Rigid-flex PCBs Built on FR-4 and Polyimide
(FPC's are custom-made products, the picture and parameters shown are just for reference)
General description
this is a type of rigid flexible printed circuit boards for the application of Wireless Security
System. It's a 3 layer rigid-flex PCB at 1.6mm thick at rigid part. the base laminate is from
Shengyi. It's fabricated per IPC 6012 Class 2 using supplied Gerber data.
Parameter and data sheet
Features and benefits
Excellent flexibility
Reducing the volume
Weight reduction
Consistency of assembly
Increased reliability
Controllability of electrical parameter design
the end can be whole soldered
Material optionality
Low cost
Continuity of processing
Professional and experienced engineers
Eligible products rate of first production: >95%
Application
Laser head FPC,POS antenna soft board, tablet keypad flex board
Variety of PCBs
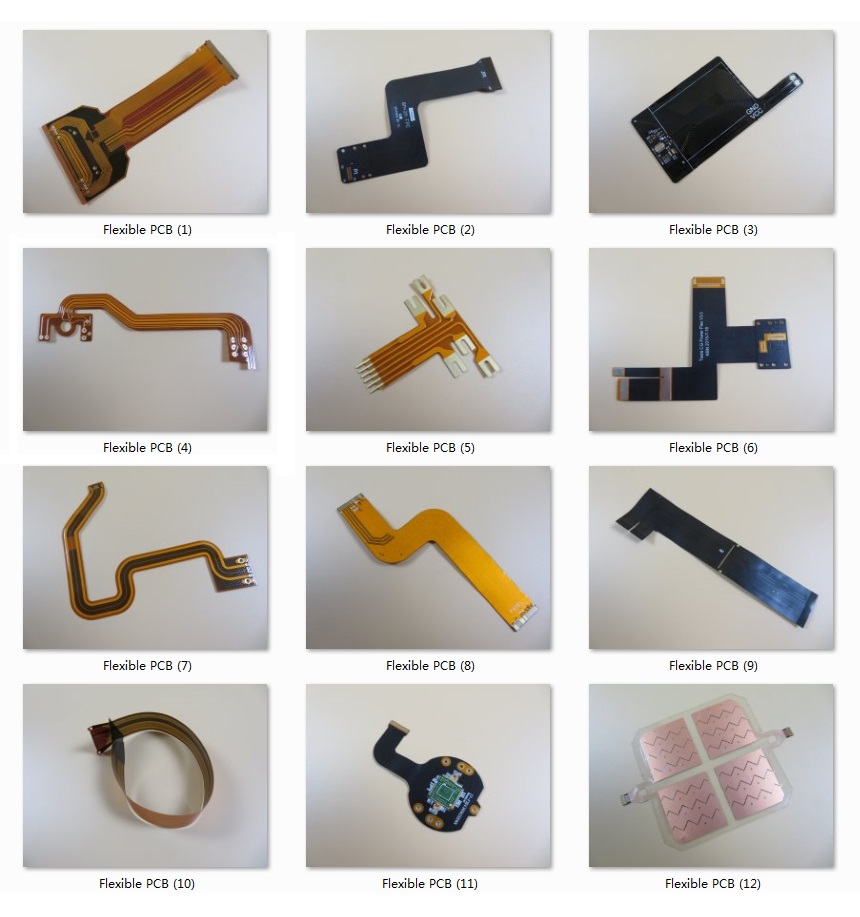
V-cut depth tester
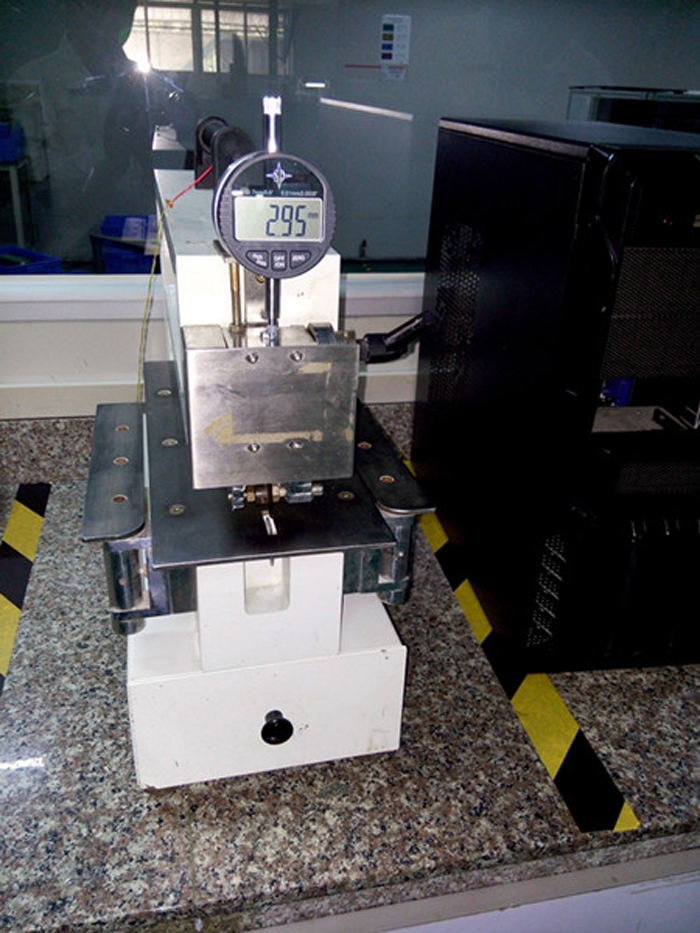
According to the number of layers of conductive copper foil, FPC can be divided into single
Layer circuit, double layer circuit, multi-layer circuit, double sided and so on.
Single-layer structure: the flexible circuit of this structure is the simplest structure of the
Flexible PCB. Usually the base material (dielectric substrates) + transparent rubber(adhesive)
+ copper foil is a set of purchased raw materials(semi-manufactures), the protective film and
Transparent glue are another kind of bought raw material. First, copper foil must be etched to
Obtain the required circuit, and the protective film should be drilled to reveal the corresponding
Pad. after cleaning, the two are combined by rolling. Then the exposed part of the pad
Electroplated gold or tin to protect. In this way, the big panel board will be ready. Generally
Also it's stamped into the corresponding shape of the small circuit board. There is also no
Protective film directly on the copper foil, but printed resistance soldering coating, so that the
Cost will be lower, but the mechanical strength of the circuit board will become worse. unless
the strength requirement is not high and the price needs to be as low as possible, it is best to
Apply the protective film method.
Double layer structure: when the circuit is too complex to be wired, or copper foil is needed
to shield the ground, it is necessary to choose a double layer or even a multilayer. the most
Typical difference between a multilayer and a single plate is the addition of a perforated structure
to connect the layers of copper foil. the first process of transparent rubber + base material +
Copper foil is to make holes. Drill holes in the base material and copper foil first, clean and then
Plated with a certain thickness of copper. the subsequent fabrication process is almost the same
as the single-layer circuit.
Double sided structure: both sides of the double sided FPC have pads, mainly used to connect
Other circuit boards. Although it and monolayer structure is similar, but the manufacturing
Process is very different. Its raw material is copper foil, protective film and transparent glue.
the protective film should be drilled according to the position of the pad first, then the copper
Foil should be affixed, the pad and track lines should be etched and then the protective film
of another drilled hole should be affixed.
Copper foil is available in two different types of copper: ED Copper and RA copper.
ED copper is an electro-deposited (ED) copper foil produced in the same way as the copper
Foil used for rigid printed circuit boards. this also means that the copper is " treated", i.e., it
Has a slightly rough surface on one side, which ensures a better adhesion when the copper
Foil is bonded to the base material.
RA copper is a rolled and annealed copper foil produced from electrolytically deposited cathode
Copper, which is melted and cast into ingots. the ingots are first hot-rolled to a certain size and
Milled on all surfaces. the copper is then cold-rolled and annealed, until the desired thickness
Is obtained.
Copper foil is available in thickness of 12, 18, 35 and 70 m.
the most common available for dielectric substrate and coverlay is polyimide films. this
Material can also be used as coverlay. Polyimide is best suited for flexible circuits because
of its characteristics as stated below:
High temperature resistance allows soldering operations without damaging the flexible
circuits
Very good electrical properties
Good chemical resistance
Polyimide is available in thicknesses of 12.5, 20, 25 and 50 m.
Base laminates for rigid printed circuit boards are copper foils laminated together with the
Base materials, the adhesive coming from the prepreg material during lamination. Contrary
to this is the flexible circuit where the lamination of the copper foil to the film material is
Achieved by means of an adhesive system. It is necessary to distinguish between two main
Systems of adhesive, namely thermoplastic and thermoset adhesives. The choice is dictated
Partly by the processing, and partly by the application of the finished flexible circuit.
FPC Case: Rigid-flex PCBs Built on FR-4 and Polyimide
(FPC's are custom-made products, the picture and parameters shown are just for reference)
General description
this is a type of rigid flexible printed circuit boards for the application of Wireless Security
System. It's a 3 layer rigid-flex PCB at 1.6mm thick at rigid part. the base laminate is from
Shengyi. It's fabricated per IPC 6012 Class 2 using supplied Gerber data.
Parameter and data sheet
Size of Flexible PCB | 91.5X 105.3mm |
Number of Layers | 3 |
Board Type | Rigid-flex PCB |
Board Thickness | 1.6mm |
Board Material | Polyimide (PI) 25m |
Board Material Supplier | Shengyi |
Tg Value of Board Material | 60 |
PTH Cu thickness | 20 m |
Inner Iayer Cu thicknes | 35 m |
Surface Cu thickness | 35 m |
Coverlay Colour | Yellow / Green Solder mask |
Number of Coverlay | 2 |
Thickness of Coverlay | 25 m |
Stiffener Material | NO |
Stiffener Thickness | N/A |
Type of Silkscreen Ink | IJR-4000 MW300 |
Supplier of Silkscreen | TAIYO |
Color of Silkscreen | White |
Number of Silkscreen | 1 |
Peeling test of Coverlay | No peelable |
Legend Adhesion | 3M 90 No peeling after Min. 3 times test |
Surface Finish | Immersion Gold |
Thickness of Nickle/Gold | Au: 0.03m(Min.); Ni 2-4m |
RoHS Required | Yes |
Famability | 94-V0 |
Thermal Shock Test | Pass, -25125, 1000 cycles. |
Thermal Stress | Pass, 3005,10 seconds, 3 cycles. No delamination, no Blistering. |
Function | 100% Pass electrical test |
Workmanship | Compliance with IPC-A-600H & IPC-6013C Class 2 |
Features and benefits
Excellent flexibility
Reducing the volume
Weight reduction
Consistency of assembly
Increased reliability
Controllability of electrical parameter design
the end can be whole soldered
Material optionality
Low cost
Continuity of processing
Professional and experienced engineers
Eligible products rate of first production: >95%
Application
Laser head FPC,POS antenna soft board, tablet keypad flex board
Variety of PCBs
V-cut depth tester