Product: | Household Product |
---|---|
Product Material: | Steel |
Shaping Mode: | Plastic Injection Mould |
Brand Name: | Odin Mould |
material: | steel |
Place of Origin: | China (Mainland) |
Quick Details
Specifications
Auto parts car front bumper mold plastic injection mold
1: Determination of bumper shell material
Regulatory requirements: the front and rear protection devices of the car must ensure that the vehicle will not cause serious damage to the vehicle when a light collision of 4km / h occurs. in addition, the front and rear bumpers not only protect the vehicle and reduce vehicle damage, but also protect pedestrians and reduce the injuries to pedestrians in the event of a collision. Therefore, the shell material of the bumper should have the following characteristics:
1) with less surface hardness, it can reduce pedestrian injuries;
2) Good elasticity and strong resistance to plastic deformation;
3) Good vibration damping effect, can absorb more energy in the elastic range;
4) Resistant to humidity and dirt;
5) Has good acid and alkali resistance and thermal stability.
Modern car bumper shells are mostly made of plastic or fiberglass. in order to reduce the cost of trial production, save mold production costs, and also shorten the trial production cycle, in the concept car trial production, consider using FRP glass fiber reinforced epoxy hand lay-up process.
the materials of the bumper are generally PP + EPEM + T20 or PP + EPDM + T15. EPDM + EPP is also more versatile. ABS uses less and is more expensive than PP. the thickness of the bumper is usually 2.5-3.5mm, and the gas-assisted molding can be made thinner.
Note that if the bottom mesh of the bumper is integrated with the bumper, the thickness of the mesh must be more than 2.0mm, and the die angle should be increased as much as possible (2 degrees or more). If the mesh is separate, the mesh wall of 1-1.5mm is sufficient.
2: Ergonomic check needed for bumper design
First, the vehicle's passability. Second, the license check. Third, check the air intake area. 4. Checking at low speed 5. Pedestrian protectionFeasibility of tow hook work.
with the popularization of automobiles, the safety of automobiles has received increasing attention, and the requirements of regulations on automobile safety will become higher and higher. At the same time, the increasingly serious energy crisis also requires cars to be as lightweight as possible. how to make occupants and pedestrians safer, to make cars less susceptible to damage during a collision, and how to minimize the weight of parts and components are more issues that need to be considered when designing bumpers.
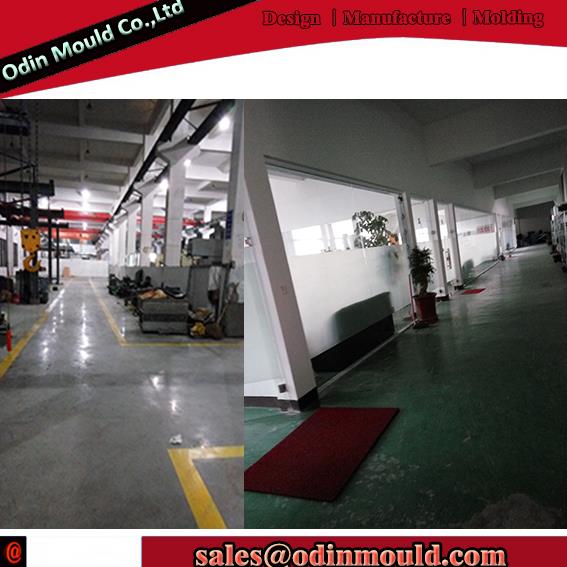
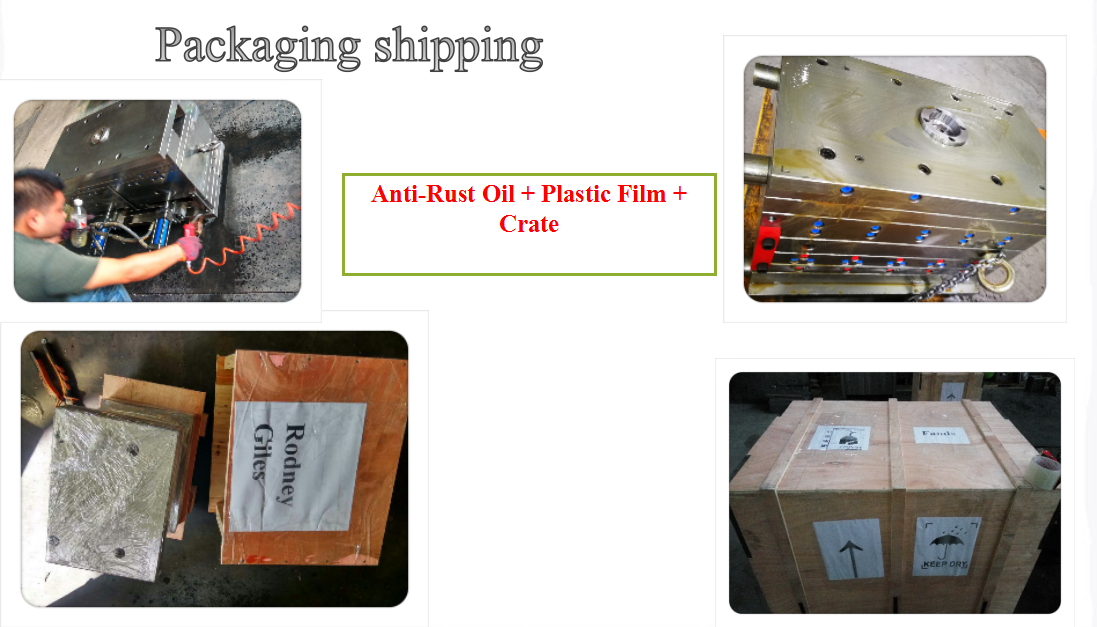
A car bumper is a safety device that absorbs and mitigates external impact and protects the front and rear of the vehicle body. Generally consists of plastic bumpers, cushioning materials and beams. Plastic bumpers have strength, rigidity, and decorativeness. from a safety point of view, a car can play a cushioning role in the event of a collision and protect the front and rear body. from the appearance, it can be naturally combined with the car body to form a natural One body, with good decoration, has become an important part to decorate the appearance of the car.
1: Determination of bumper shell material
Regulatory requirements: the front and rear protection devices of the car must ensure that the vehicle will not cause serious damage to the vehicle when a light collision of 4km / h occurs. in addition, the front and rear bumpers not only protect the vehicle and reduce vehicle damage, but also protect pedestrians and reduce the injuries to pedestrians in the event of a collision. Therefore, the shell material of the bumper should have the following characteristics:
1) with less surface hardness, it can reduce pedestrian injuries;
2) Good elasticity and strong resistance to plastic deformation;
3) Good vibration damping effect, can absorb more energy in the elastic range;
4) Resistant to humidity and dirt;
5) Has good acid and alkali resistance and thermal stability.
Modern car bumper shells are mostly made of plastic or fiberglass. in order to reduce the cost of trial production, save mold production costs, and also shorten the trial production cycle, in the concept car trial production, consider using FRP glass fiber reinforced epoxy hand lay-up process.
the materials of the bumper are generally PP + EPEM + T20 or PP + EPDM + T15. EPDM + EPP is also more versatile. ABS uses less and is more expensive than PP. the thickness of the bumper is usually 2.5-3.5mm, and the gas-assisted molding can be made thinner.
Note that if the bottom mesh of the bumper is integrated with the bumper, the thickness of the mesh must be more than 2.0mm, and the die angle should be increased as much as possible (2 degrees or more). If the mesh is separate, the mesh wall of 1-1.5mm is sufficient.
2: Ergonomic check needed for bumper design
First, the vehicle's passability. Second, the license check. Third, check the air intake area. 4. Checking at low speed 5. Pedestrian protectionFeasibility of tow hook work.
with the popularization of automobiles, the safety of automobiles has received increasing attention, and the requirements of regulations on automobile safety will become higher and higher. At the same time, the increasingly serious energy crisis also requires cars to be as lightweight as possible. how to make occupants and pedestrians safer, to make cars less susceptible to damage during a collision, and how to minimize the weight of parts and components are more issues that need to be considered when designing bumpers.